|
|
#lakesidepottery
|
|
Many people use a certain temperature (Cone number) for bisque firings, because of habit but not because they have thought about it. So what are the various factors to consider in deciding how hot to bisque fire your ware?
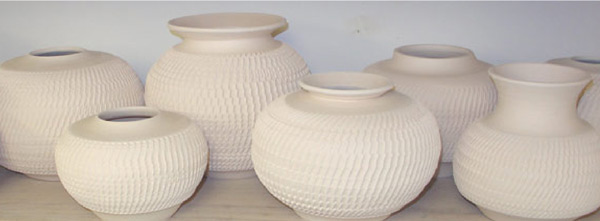
The strategies involved in low fire and high fire are actually opposite.
Low Fire: In low fire, the bisque temperature is usually hotter than the firing temperature. For example, most commercial glazes recommend bisque firing to Cone 04, and glaze firing to Cone 06 (which is cooler.) The reason for this is to make sure all the carbon and other materials in the clay burn out during the bisque firing. If you glaze fired to a hotter temperature than the bisque, it is possible that more carbon would burn out during glaze firing, causing blisters in the glaze which would not have time to heal over.
For some clays this is not a problem. The carbon content in the clay is low or burns out early. Because of the convenience of having bisque and glaze in the same kiln load, I have always bisque fired my low fire pieces at Cone 06, and glaze fired them at Cone 06. I have not had any problems. But I have heard of other people having problems so it is a possibility.
Another reason that low fire bisquing is done differently than high fire, is that glaze is typically brushed or sponged on, not dipped. So the amount of glaze you add is less dependent on the porosity of the clay, and more on how you brush it on.
High Fire: Different people have different strategies here, but by understanding them you will be able to make an informed decision.
The first principle is that you want to bisque low so that the ware is still very porous and can absorb glazes.
The second principle is that you want to bisque hot enough that your piece doesn't absorb too much glaze resulting in it being too thick or actually causing the piece to fall apart. In fact, this is the main reason to bisque at all.
So between these two extremes you need to settle on a bisque firing temperature. I have found that most potters bisque somewhere between Cone 010 and Cone 04, with Cone 06-08 as the most common.
Pros and Cons at the high end.
At Cone 04, you may have problems with the pot not absorbing enough glaze. This is particularly true if you do glaze layering. However, the ware is stronger when fired to Cone 04. So you have less chance of dunting (cracking) during the cooling, which can be a big problem with large or porcelain ware. In addition, you will have burned out more of the carbons, which might give better results with certain clays and glazes.
If you are bisquing to Cone 04, you have to use your glazes at a thicker consistency. This can be useful because thicker glazes don't settle out as fast. However, even though ware is stronger (more resistant to breaking) when bisqued at higher temperature, it is actually more sensitive to thermal shock because it is less porous and less flexible. Therefore, when doing Raku you might want to bisque at a lower temperature so you have more resistance to thermal shock. However, the right clay body also will take care of this for you so if you use the right clay it isn't an issue.
Pros and Cons at the low end.
At Cone 010 or lower, the piece may absorb too much glaze, and it is less strong (easier to crack accidentally in handling, and more likely to crack from dunting during cooling.) But it is more resistant to thermal shock.
So, what to do?
If you already use a bisque temperature and it seems to be working, there is no need to change it. In fact if you do change it, you may need to adjust the thickness of your glazes.
If you don't have a bisque temperature, or if you are changing clays, the best advice is to start at Cone 08 to Cone 06. From there you can adjust up or down using the principles described above. Some specific indications that you should change your bisque temperature are: If your bisqued piece does not absorb glaze well, so the glaze sits on the top of the pot for a long time without drying, then try bisquing to a lower temperature. If your clay bloats during glaze firing, try raising the temperature of your bisque firing to burn off more carbonous material in the clay.
And don't worry too much about it. Most clays and glazes have a pretty wide range that will work fine.
Firing electric kiln (kilnsitter and computereized)
Clay drying and firing process
|